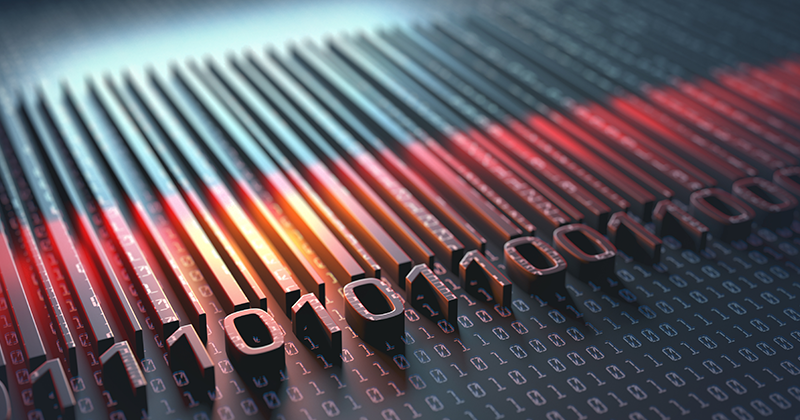
INTRODUCTION
Barcodes and other automatic identification and data capture (AIDC) technologies are ubiquitous in everyday life. They are found everywhere from grocery stores to passports because they are mature, proven, and less expensive than they once were. Essentially, if you have not found a way to utilize them in your materials management function, you are missing out on worthwhile benefits and stuck in a paper-intensive manual world. AIDC technologies have been used in some capacity since the 1950s, yet today there are still opportunities for adoption. As the internet of things (IoT) and advanced connectivity technologies (e.g., 5G, low Earth orbit satellites) are adopted, AIDC becomes more important than ever to compete with the best-in-class companies and align with materials management leading practices.
At its core, automatic identification is simple. A set of symbols or signals is encoded so it may be read by a machine or processor and associated to an item as a barcode label or tag. A scanner “reads” the data so it can be decoded back to alphanumeric characters for later use. Automatic identification technologies feature different shapes and sizes and are designed for different uses.
Example AIDC Technologies:
![]() |
Barcode: A machine-readable code in the form of numbers and a pattern of parallel lines of varying widths. It is the most prevalent in materials management functions. | |
![]() |
Radio Frequency Identification (RFID): Unlike barcodes, RFID does not require line of sight or contact to be read by the host software. | |
![]() |
QR Code: A machine-readable code consisting of an array of black and white squares. It is typically used for storing more information than a barcode. | |
![]() |
Biometrics: This technology compares captured biometrics such as fingerprints, iris patterns, and voice recognition and uses that information to validate/capture user information. | |
![]() |
Smart Card/Magnetic Strip: Stores personal information via chip or magnetic stripe. | |
Example Use Cases for AIDC Technologies:
![]() |
Receiving Operations: Scan case-level barcodes and associate those items to the pallet on which they are placed. Also work with the suppliers to associate AIDC-tracking data with advanced shipping notices to measure inbound work before it hits your dock. | |
![]() |
Directed Stockkeeping and Replenishment: Direct the staff to a specific location and verify the correct location. Confirm that the right items are being replenished from and to the right locations. | |
![]() |
Work Completion and Quality Control: Direct a worker to a location to perform a task and require confirmation of both. Provide confirmation that the right item has been picked. | |
![]() |
Cycle Counting: Conduct automated cycle counting using RFID where vehicles travel autonomously through the warehouse receiving RFID data. | |
AIDC DELIVERS MANY BENEFITS
There are a number of materials management operations that feel stuck in the past. Many of them have manual and paper-intensive processes. The staff in these operations are fully aware that there are AIDC options to improve operations where the investment required is low; however, leadership has not prioritized improving how work is completed in materials management. Often the benefits are measured in labor savings, and AIDC solutions may only provide fractional FTEs. Visibility of SKUs, error reduction, inventory accuracy, improved operational control, and reductions in work in process are among the many additional benefits of an AIDC technology solution that should be considered in the decision to invest, depending on the use case.
SCOTTMADDEN’S KEY CONSIDERATIONS FOR DEPLOYING AIDC SYSTEMS
Often leaders feel a mandate to seek technology solutions to improve their operations. Looking for a silver bullet can be a mask that causes leaders to overlook or discount the rigor in identifying business requirements and aligning processes with leading practices. Solution providers will bring a focus on costs and expected returns. Balancing all of these considerations with an agnostic third party is a healthy and balanced way to ensure you choose the right solution that can be configured to meet the objectives of the operation.
Four Considerations for Implementing AIDC Technologies:
- Identification of Business Requirements: A current state assessment will help identify specific technological (e.g., RFID, barcodes) and process needs (i.e., level of tracking – SKU, box, each) for each warehouse and ensure alignment with materials management strategy.
- Leading Practice Alignment: Does the chosen solution align with industry leading practices?
- Costs: The costs to deploy an AIDC system can vary by location and desired specifications (e.g., passive vs. active RFID tags, number of readers) that fit the needs of each warehouse. Typical costs break down as follows: tags/sensors (10%), hardware (15%), software (40%), services (25%), support (10%).
- Expected Returns: The expected returns vary by project and technologies deployed. Past projects and RFID studies have delivered 80% improvement on shipping and picking accuracy, 30% improvement in inventory accuracy, 90% improvement in receiving time, 80% reduction in lost tools/materials, and 30% reduction in inventory carrying costs. Payback periods are often less than two years.
INVESTING IN AIDC TODAY TO PREPARE FOR AN INTERNET-OF-THINGS FUTURE
With the emergence of IoT and inexpensive sensors that can be deployed everywhere, AIDC plans should also consider the future, which may include extending their existing systems and getting the added benefits of IoT. Major AIDC providers are working to integrate legacy and smart devices to the internet with cloud-based platforms, essentially creating a bridge from AIDC to IoT. AIDC is a fundamental building block of IoT.
HOW SCOTTMADDEN CAN HELP
Below is a high-level summary of our four-step approach to plan your AIDC implementation. It is important to establish a baseline during Step 1 to assess the current operational process and understand the technology integration options with your ERP or warehouse management system. A key feature of the approach is to pilot the solution in a small subset of your operation and review the results of the pilot against the assessment baseline so you can refine and adjust. Our consultants can help mitigate the risk that the solution does not achieve the expected benefits and there are not unintended operational consequences (e.g., ID tags not standing up to environmental conditions, data access points not positioned or capable for efficient data transmission).
![]() |
Step 1: Assess
|
|
![]() |
Step 2: Design and Prototype
|
|
![]() |
Step 3: Monitor Results and Adjust
|
|
![]() |
Step 4: Implementation
|
CONCLUSION
AIDC technologies are now a staple in efficient supply chain operations after a half century of adoption and improvements. Warehouses without AIDC tend to be more expensive and less efficient relative to their industry peers, especially if they are manual and paper intensive. With each passing day, materials management operations that are not adopting these solutions are being left behind, and equally as important, they are not preparing for the future capabilities that IoT provides. To determine the best way to implement AIDC, executives must consider the right technology for their organization, their needs, and their unique set of circumstances. ScottMadden can help—our approach is coordinated and relies on understanding your current baseline, setting up a pilot, and refining the solution to achieve the results you desire.