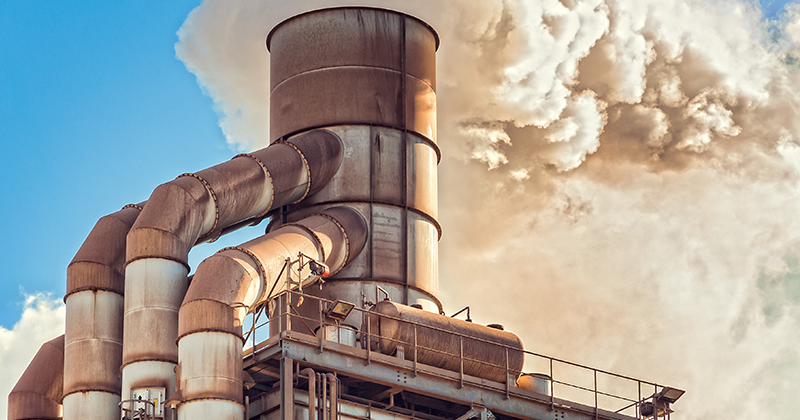
As investors and consumers increase their focus on sustainability, establishing carbon reduction or net-zero goals has become table stakes among industry leaders. According to a recent report from Data-Driven EnviroLab and the NewClimate Institute, the number of businesses that established net-zero goals increased threefold from 500 at the end of 2019 to more than 1,500 during the first nine months of 2020. Many of these net-zero pledges target full decarbonization by 2050, quickly becoming the benchmark for company climate pledges.
As more and more companies establish ambitious carbon reduction and net-zero goals, these goals must be established using science-based analysis and targets for carbon accounting. Companies that define carbon-reduction goals not based on detailed analysis run the risk of setting unrealistic targets and could be more susceptible to accusations of greenwashing.
What is Carbon Accounting?
Carbon accounting is the process of identifying and quantifying an organization’s carbon emissions that are associated with its operations. Once an organization understands the sources of its emissions, it can use that information to identify emissions hotspots, propose reduction opportunities, and establish attainable reduction targets. Before setting any carbon reduction goals or developing a roadmap to achieve targets, organizations must first understand their emissions profile.
The Greenhouse Gas Protocol’s Carbon Accounting Framework, based on standards by the World Resources Institute and the Business Council for Sustainable Development, is widely used and considered a best practice for carbon accounting. However, the framework and accompanying standards extend beyond carbon dioxide and include other greenhouse gas emissions (GHGs) like methane, nitrous oxide, hydrofluorocarbons, perfluorocarbons, sulfur hexafluoride, nitrogen trifluoride. Companies then translate these other GHGs into carbon equivalents, or CO2, based on their global warming potential (or GWP) to allow for reporting in a common unit. For simplicity, we will refer to all GHGs as carbon emissions.
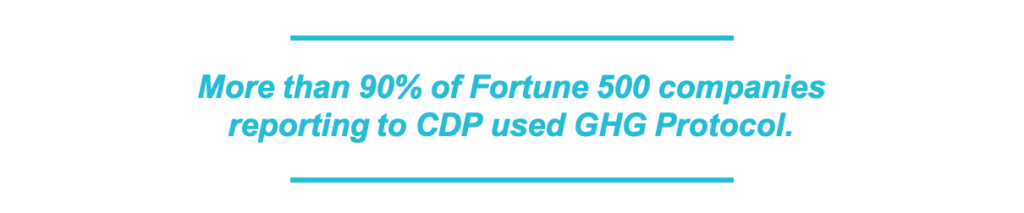
The Carbon Accounting Process: Which Emissions Should be Counted?
The Greenhouse Gas Protocol classifies an organization’s carbon emissions into three scopes:
- Scope 1: Direct emissions from sources owned or controlled by the company – typically from manufacturing, on-site power generation from fossil fuels (e.g., diesel generator, natural-gas-fired boiler, etc.), production/manufacturing equipment, vehicles, etc.
- Scope 2: Indirect emissions from the purchase of electricity, steam, and heating/cooling generated by carbon-emitting resources. While Scope 2 emissions are typically the easiest to calculate as data can be provided by the company’s utility or power producer, additional assumptions must be made when companies rent building spaces that are not sub-metered.
- Scope 3: All other indirect emissions that occur in the company’s value chain. The source of Scope 3 emissions varies significantly by industry. Some examples include business travel, third-party distribution of products, consumption of sold products (e.g., gasoline), employee commuting, disposal of sold products, company investments, etc. These emissions are often the most complex to identify and calculate as the majority are typically not controlled directly by the company (e.g., a textile manufacturer typically cannot control the fuel used in their third-party distribution vendors’ vehicles or aircraft). Some companies include a thorough Scope 3 accounting, while others define Scope 3 in a more limited manner; either practice is acceptable as long as the company is transparent in its methodology.
Companies starting on decarbonization strategies will often focus on areas they can more easily control—Scope 1 and 2 emissions. That said, many stakeholders now expect a robust discussion and accounting of Scope 3 emissions. For example, the Science Based Target Initiative requires companies to account for Scope 3 emissions if they are likely to account for 40 percent or more of total emissions.
Case Study: Textile Manufacturer
Fully understanding the three scopes of emissions and how they apply to companies can be challenging. Therefore a simplified example of the sources of carbon emissions for a textile manufacturer has been developed to provide additional context. In this simplified example, the reporting company (shown in grey):
- Purchases all raw materials from third parties
- Owns and operates one factory to manufacture clothing and several trucks to deliver finished products to a third-party distributor
- Uses a third-party distributor to store and deliver its final product to end-use consumers
- The image below outlines the sources of carbon emissions for the reporting company over the life cycle of its products.
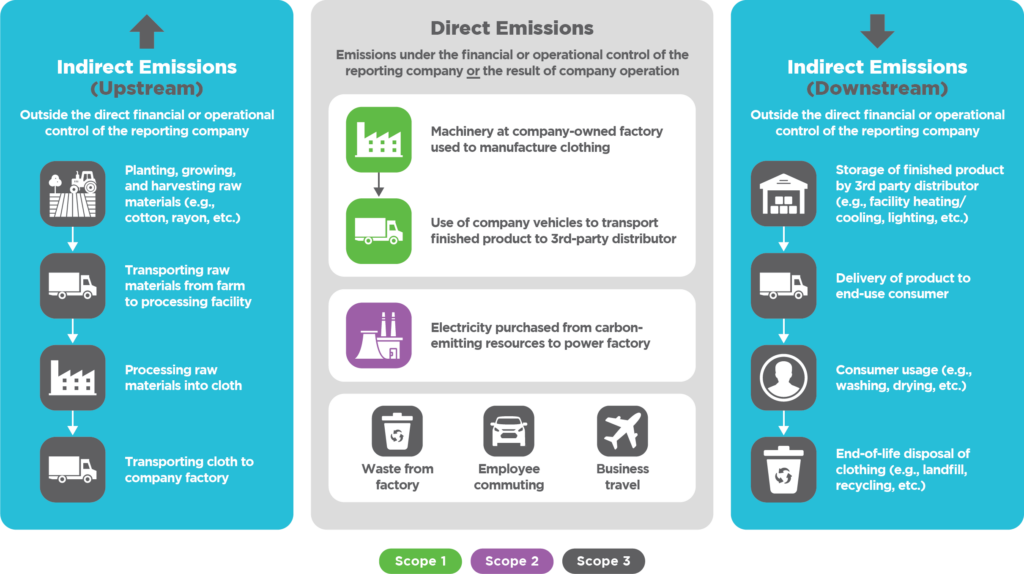
In this simplified example, there are apparent lines between direct and indirect emissions for the reporting company. In reality, the companies that operate in this industry will likely have the following:
- More facilities (i.e., a mix of office buildings and manufacturing facilities often spread across a wide geographic footprint);
- A more integrated supply chain (i.e., involved in the growing/processing of raw materials, transportation of raw materials, storage of completed product, etc.);
- A corporate structure with multiple operating companies/subsidiaries, etc., that will add additional complexity to the process.
Where to Start?
Once a company decides to focus on reducing carbon emissions, it must begin a formal inventory. Regardless of industry, there are a few basic steps that a company can take to identify and quantify its emissions formally.

Step 1: Identify Boundaries
Carbon Accounting depends on company structure (i.e., standalone entity, part of a joint venture, partially/wholly owned subsidiary, etc.) and the extent to which it has operational or financial control over emissions sources (e.g., company fleet vehicles versus employee-owned vehicles). These two boundaries are referred to as organizational boundaries and operational boundaries, respectively, under the GHG Protocol. Though there are several acceptable methodologies to identify these boundaries, the end goal is to ensure that carbon emissions can be consistently attributed to the appropriate entity and categorized into the proper scope to avoid double or undercounting emissions.
Step 2: Identify Emission Sources and Scopes
Once boundaries have been established, companies then identify emission sources and categorize them by scope. The level of effort required varies considerably based on the size of the company, the industry or industries in which it operates, and the extent of its upstream and downstream activities. In addition, significant emissions are often not under the company’s direct control, requiring more effort to adequately identify indirect emissions associated with company operations and identify appropriate data sources.
Step 3: Quantify Emissions
After identifying the sources, the carbon accounting process to quantify emissions begins. Similar to the previous step, the level of effort varies based on the scope and definition of the emissions, company size, company structure, and data availability. To ensure accuracy, carbon accounting teams should identify and involve subject matter experts most familiar with each emission source (for example, using the case study above, the fleet manager of the textile factory should be consulted when trying to quantify emissions from company-owned vehicles). Companies should use primary data from their operations whenever possible and secondary (proxy data) if primary data is unavailable. For most companies, data will be imperfect, and assumptions will be required. A carbon inventory is nearly always calculated rather than measured—what matters is transparency. Any assumptions or gaps in data should be clearly articulated in a company’s publicly available disclosures. Once all emissions have been quantified, non-carbon GHGs are typically translated into carbon equivalents.
Step 4: Incorporate Results into Operations and Strategy
Once sources of emissions have been identified and adequately quantified, companies use the results to establish or inform emissions-reduction goals (with an initial focus on high-impact and/or easy-to-address emissions sources). One potential approach for a company seeking to reduce its emissions could include the following:
- Examine potential energy efficiency solutions to reduce their overall carbon footprint
- Examine its power needs and explore “greener” options like installing on-site solar or procuring renewables through an RFP
- Evaluate offsetting the remainder of their carbon footprint by purchasing carbon offsets or unbundled renewable energy credits
For example, if the textile factory in the case study finds that an aging HVAC unit is leaking refrigerant (a GHG with significantly greater GWP than carbon), it may choose to repair or replace the unit. Repairing the unit will eliminate the release of a harmful GHG, while replacing the unit would stop the release of refrigerant and result in lower ongoing operating costs as new HVAC units increase efficiency. After this efficiency upgrade, the company may explore and evaluate additional operational changes, their power sources, or offset mechanisms to further reduce their footprint or achieve carbon neutrality.
The carbon inventory and resulting strategic decisions should be reported externally through a formal sustainability report or through other channels to communicate company performance and priorities to stakeholders.
Ongoing Maintenance
The emissions profile of a company is not a constant and should be routinely monitored and revised to account for changes over time. Routine business activities, like opening or closing a facility, upgrading equipment, engaging in a joint venture, adding on-site solar, or renegotiating a power agreement with the local utility, can all impact emissions. There is no one-size-fits-all approach for ongoing maintenance, and the level of effort varies greatly. Therefore, companies should routinely evaluate their options as to the most efficient and accurate way to monitor changes to their emissions profile.
How Can ScottMadden Help With Carbon Accounting?
Prior to setting carbon-reduction targets, companies must first fully understand the sources of emissions associated with their operations. This preparation will provide companies with data to inform the target-setting process that can be leveraged when establishing a broader strategy to reduce emissions.
Our consultants are experienced in helping clients from a variety of industries establish carbon accounting processes, develop formal emissions-reduction targets, and integrate these goals into broader corporate strategy and operations. Reach out to ScottMadden Consulting for support with your carbon accounting journey today.
Sources
- Carbon Accounting Basics: https://supplychain.edf.org/resources/carbon-accounting/
- Companies Reporting GHGs to CDP: https://ghgprotocol.org/#3
- Scopes 1 and 2: https://ghgprotocol.org/sites/default/files/Guidance_Handbook_2019_FINAL.pdf
- Scope 3: https://www.ghgprotocol.org/sites/default/files/ghgp/standards/Scope3_Calculation_Guidance_0.pdf
- Carbon Disclosure Project: https://supplychain.edf.org/partner/cdp/
- Data-Driven EnviroLab and the NewClimate Institute: https://www.greenbiz.com/article/global-net-zero-commitments-double-less-year
- Science Based Target Initiative: https://sciencebasedtargets.org/resources/files/SBTi-criteria.pdf